Thread mills of the GARANT Master TM family: Revolutionary in process reliability and performance
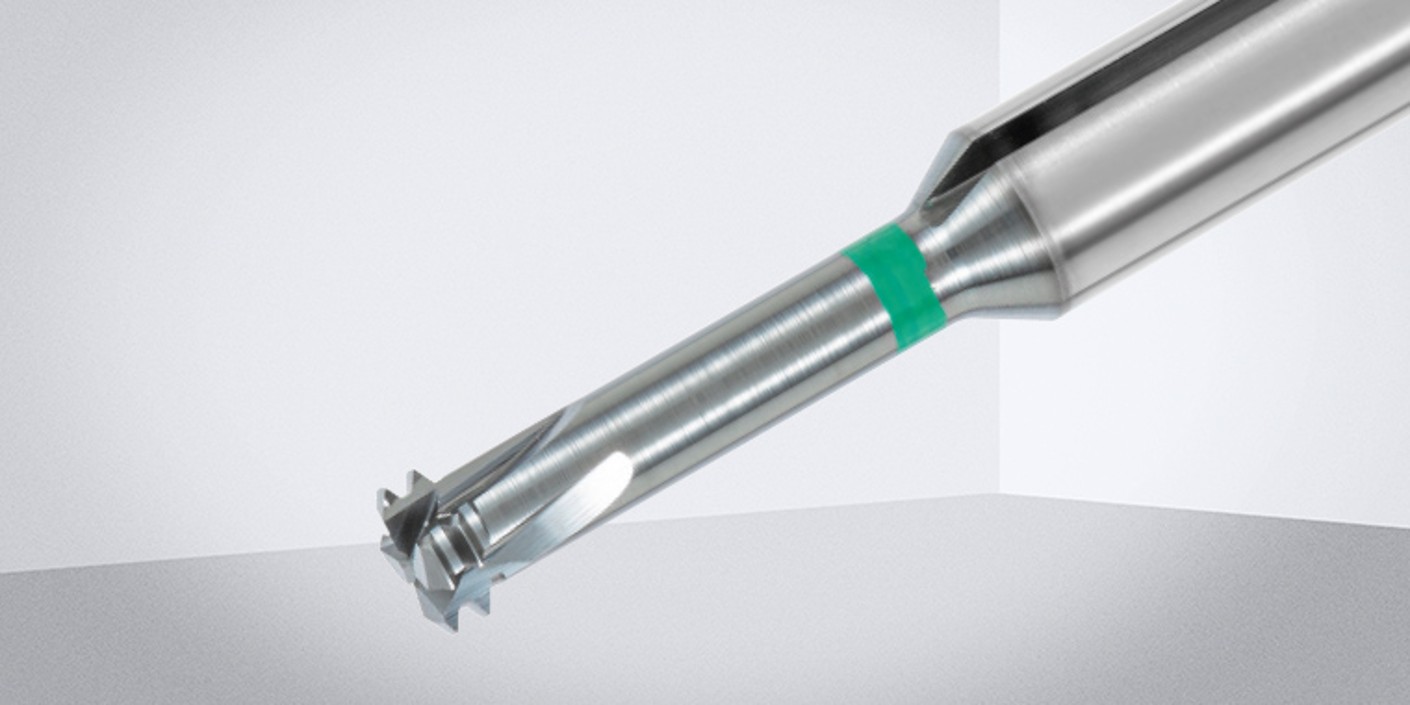
GARANT Master TM end cutting thread mill: impresses with high process reliability and long tool life
The special front cutter geometry with unequal spacing permits process-reliable circular thread milling across a wide spectrum of materials. The GARANT Master TM end cutting thread mill can be used in a wide range of industries, from automotive and mechanical engineering to aerospace.
The homogeneous solid carbide ultra-fine grain substrate ensures a consistent metal removal rate with increased tool rigidity and bending strength.
The innovative centre cutting edge geometry offers even more wear protection during full circular plunging.
Result: Long tool life without having to constantly change the tool. In addition, the higher process reliability minimizes the risk of workpiece scrap and thus avoids unwanted production delays - also with regard to long value chains.
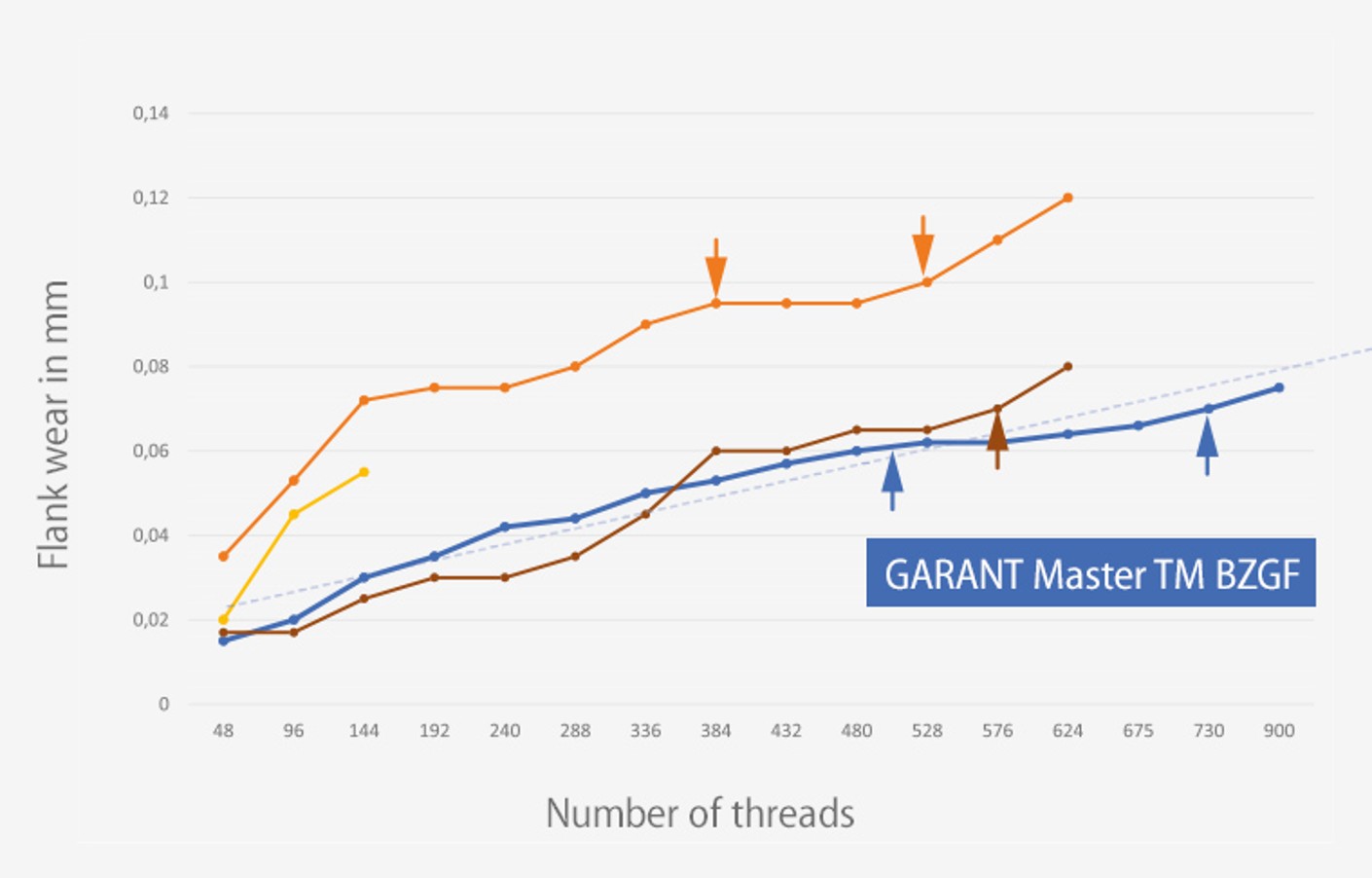
Comparison test GARANT Master TM with competitors: Tool life comparison benchmark.
Test series M6 thread 2.5×D in 1.7225 (42CrMo4+QT):
- Climb milling without divided cut.
- Direction of spindle rotation to the left (M04).
- Variable cutting values according to manufacturer’s specifications.
- Milling/thread depth = 15 mm.
- Clear advantages in terms of wear and service life in the comparison test.
GARANT Master TM | ![]() | ![]() | ![]() | ![]() |
---|---|---|---|---|
Wear after 225 threads | Wear after 450 threads | Wear after 675 threads | Wear after 900 threads | |
Competitor 1 | ![]() | ![]() | ![]() | |
Wear after 96 threads | Wear after 480 threads | Strong wear after 624 threads: End of test. | ||
Competitor 2 | ![]() | ![]() | ![]() | |
Wear after 96 threads | Wear after 480 threads | Strong wear after 624 threads: End of test. |
Your benefits at a glance
- Drilling and tapping in a single operation. Left-hand cutting tool!
- Optimal coolant delivery.
- Maximum achievable thread depth.
- High surface quality of the thread.
- Possible use in a wide range of materials. Green ring for general applications.
- Reinforced tool core for maximum process reliability.
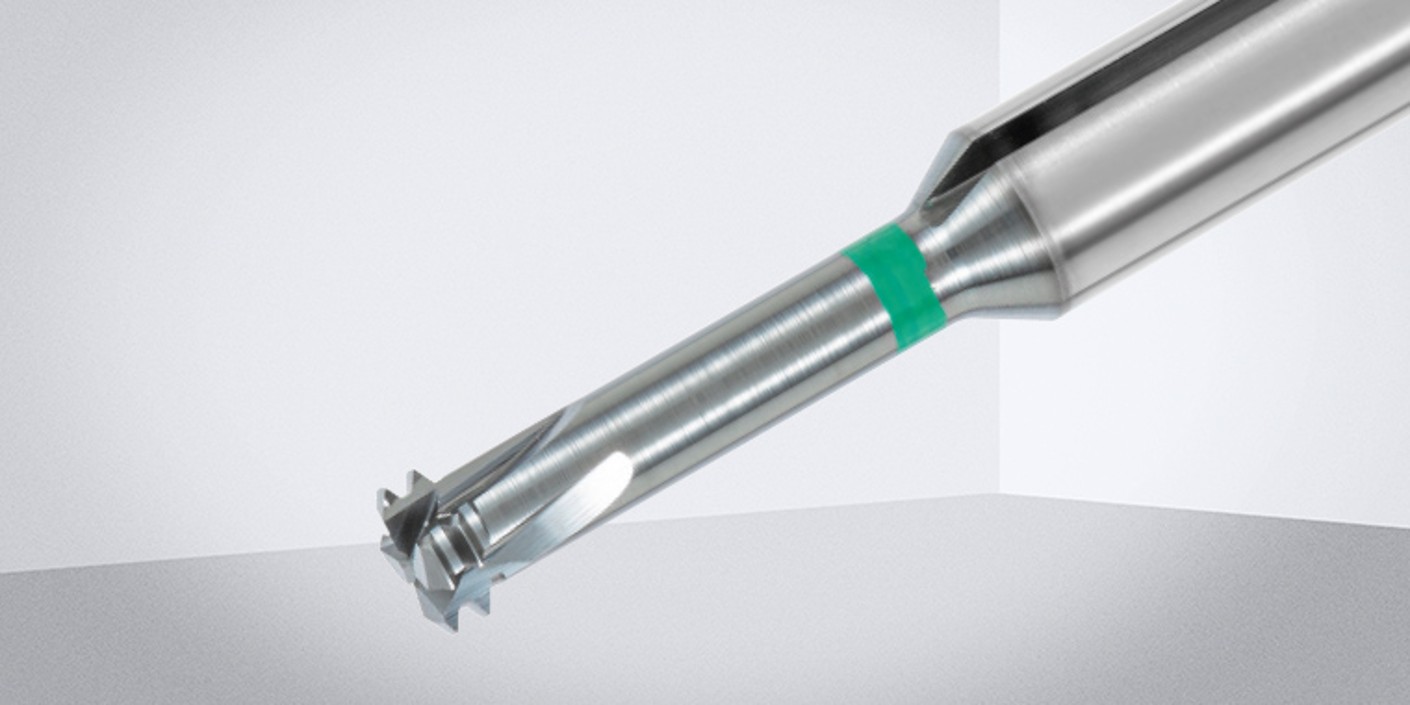
GARANT Master TM end cutting thread mill: impresses with high process reliability and long tool life
The special front cutter geometry with unequal spacing permits process-reliable circular thread milling across a wide spectrum of materials. The GARANT Master TM end cutting thread mill can be used in a wide range of industries, from automotive and mechanical engineering to aerospace.
The homogeneous solid carbide ultra-fine grain substrate ensures a consistent metal removal rate with increased tool rigidity and bending strength.
The innovative centre cutting edge geometry offers even more wear protection during full circular plunging.
Result: Long tool life without having to constantly change the tool. In addition, the higher process reliability minimizes the risk of workpiece scrap and thus avoids unwanted production delays - also with regard to long value chains.

Always the right choice for your thread milling process:
1. Unequal spacing: Significant reduction in vibration. Very smooth cutting action. Reduction in the cutting forces avoids tool displacement.
2. Corrected thread profile: Avoidance of profile distortion. Threads true to gauge and true to standard.
3. Innovative coating: The latest coating technology for optimum protection against wear. High performance over a wide spectrum of materials.
4. Increased number of cutting edges: More efficiency due to increased contour feed rate.
5. Optimised solid carbide substrate: Improved bending strength. High tool rigidity.
GARANT Master TM achieves measurable advantages in the production process

Very smooth cutting action and reduced cutting forces due to innovative geometry.
Radial cutting forces and vibration pose a major problem for the process reliability of the thread milling process. Thanks to the unequal spacing of its cutting edges, the GARANT Master TM solid carbide thread mill significantly reduces these influencing factors, as cutting force measurement impressively demonstrates.
Measuring point A: After 180° cutter entry path at entry into the wall of the hole
The measurement points for GARANT Master TM show a well-defined distribution of the bending moment. The comparison tools showed a visibly more uneven distribution, which is traceable back to heavy vibration during machining.
Measuring point B: With full engagement of the cutters
The lateral forces that arise during thread milling affect the quality of the thread. The GARANT Master TM has a clear distribution of the measurement points. Conventional thread mills tend to generate high levels of vibration, causing significantly uneven distribution of the bending moment. To some extent this leads to threads no longer true to gauge.